Re: Rug Warrior Pi: Build Blog (a PiDA bot)

You are welcome! I normally use two spacers, then the 18mm nylon spacers are at the correct height.
See this side way shot of the Pi Rtc Dio, and imagine it was Pi Droid Alpha... note how the stacking header is mounted.
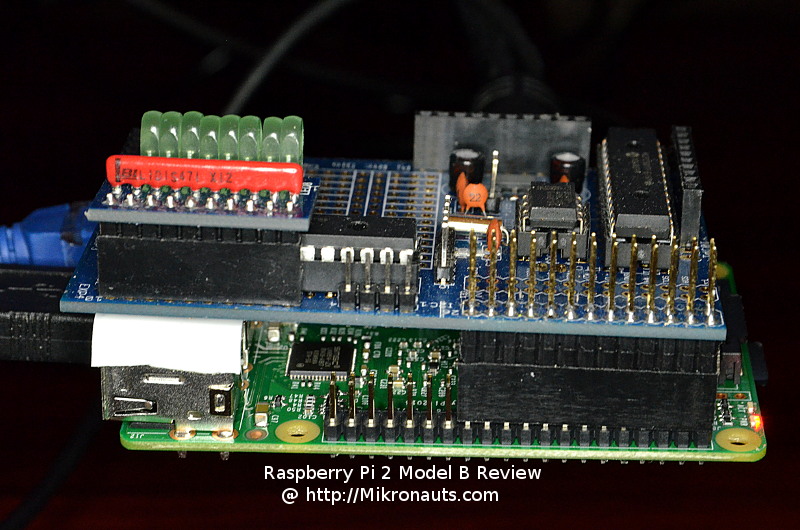
See this side way shot of the Pi Rtc Dio, and imagine it was Pi Droid Alpha... note how the stacking header is mounted.
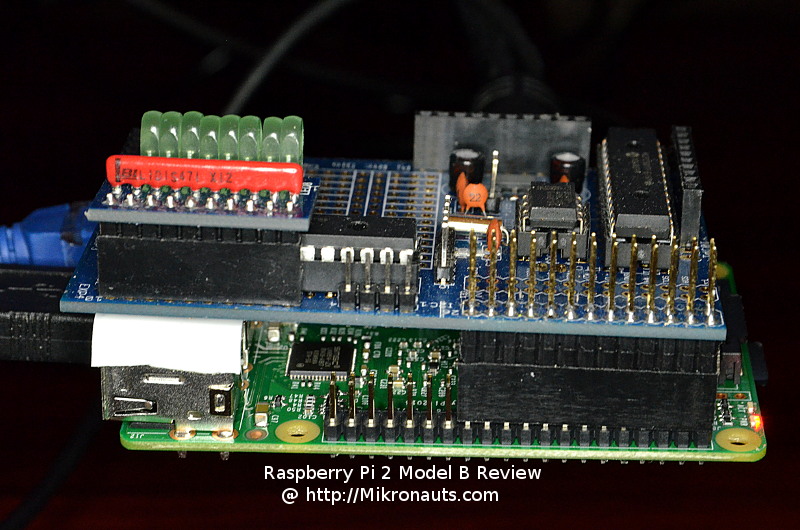
alanmcdonley wrote:mikronauts wrote:The 26 pin stacking header should be assembled to PiDroidAlpha as shown on p.15 of the assembly manual
Good catch - thanks.
I cannot tell from the manual pic or words - how many 26 pin spacers under the board?
Alan